As usual, folks ask me questions and I try to answer and when enough of you ask a similar question it results in an askJOHN . . . here's another!
Q. I’m still learning and had a 2S 2000mAh LiPo in my 48” Extreme Flight Extra and it went dead. Discharged too low because of an electronic switch (low parasitic draw, but a discharge, nonetheless).
So for three or four 5-minute flights, I’m thinking two of your B2S2000 packs connected using a diode and switch for each.
I also need packs for my 90” Super Stearman (a gasser with 7 servos powered by a sweet Saito 123). I’m figuring two of the B2S5000 and again, each with its own switch and diode system. What are your thoughts?
A. So you're still learning, eh? Good, me too! Life long mission. OK, maybe you can learn a little something from me, here goes . . .
First, batteries don't need a back up. Instead, I advise using one battery with two leads. Why two leads? Simple, because it lets you use two switches in parallel. So why two switches in parallel? For safety, silly! After all, from statistics we learn odds of both switches failing on the same flight are astronomical.
So math is what protects you, not toting the dead weight of a spare battery pack and certainly not those $50 snake oil switches. Speaking of which, I favor inexpensive mechanical switches versus pricey electronic switches, but I digress.
Second, how much battery do you need? As a wise wag put it . . . it depends. Use this to guide you;
- One B2S850 for your 48-60" models.
- Similarly, one B2S2000 for 74-85" models
- And one B2S5000 for anything with lots of servos.
Note, we also offer alternative chemistry packs; LiFePO4 as well as LiIon. These are rated at 1500, 3000, and 6000mAh instead of 850, 2000, and 5000mAh.
- Battery packs are available in various lithium-based chemistries
Regarding chemistry
So what's different? LiFePO4 packs have lower pack voltage 'but' a much greater safety margin 'and' the tremendous benefit of allowing you to leave them fully charged instead of putting them at storage voltage when they're not being used. This means if you plan to fly and weather (or a honey-do) interferes with going to fly, then instead of going to the trouble of discharging the pack to storage voltage (as you should for LiIon and LiPo packs), then you can safely leave them fully charged. For how long? Don't know but from experience I know I can safely use the pack without recharging - for even a year before going to fly my model because the discharge rate is so very low! Yes, LiFePO4 costs a bit more than LiIon packs but I love them for most models.
Note, I use LiFePO4 for my own personal models, but you have to spec the servo torque appropriately. What's this mean? The trick for these is to calculate servo-torque based on LiFePO4 discharge voltage instead of on a LiIon's. This because the latter form the basis of the spec used to put lipstick on the pig to sell servos.
Anyway, while I can't speak for other servo manufacturers, these are figures we fully disclose within the servo specs tab for all of our servos. Below, for example, is the spec sheet for the popular DS360DLHV.
- Note; performance specs are arranged by voltage arrayed in columns
Basically, use the 8.4V column for LiIon and the 6.6V column for LiFePO4. The 5V and 6V columns are for old-school nickle-based chemistry (4-cell and 5-cell, respectively), while the 7.4V is for those who like calculating based on nominal voltage. Yes, we could complicate things further but we don't want to confuse folks.
Summary
One, a single battery is enough. Second, use two switches for safety (mechanical type, leave the fancy electronic switches for those who never progressed beyond counting on their fingers). Three, rely on the servo-specs chart to determine which servo you need based on voltage characteristics, not the specs advertised to sell servos to the simple minded.
Bonus thoughts
I hate switches. Damned things are what fail most often in my experience. More so than receivers, servos, or batteries. Batteries are actually the most reliable . . . two cells and a lead beat the hell out of 30 components in a servo or receiver in terms of reliability. Number of components matter for this calculation. Always has, always will.
I detest so-called smart switches for my model airplanes. Give me a cheapo mechanical slide switch every time. Either it works, or it doesn't but there's no maybe to it. Electronic switches supposedly are the cat's meow but what the sellers of these things never tell you is this; what happens when the component that assures it stays on goes teats up? That's right, you're back to a single point of failure. Me? I prefer to put my trust in mathematics. And two switches in parallel beats Hell out of one magic switch.
Third, regarding the best switch possible? None at all. Or more accurately, two non-existent switches. Huh? Yup, I am ruthless about eliminating switches because I prefer to use a couple of short extension between the receiver and the battery leads. Thus, 'I' make/break the connection when I want to fly. Put another way, I become the switch!
The way this works is simple; connect one extension to the port marked BAT on the receiver case. Connect the other to any free port (channel) on the receiver. Since receivers feature what's called a power bus, then the (+) and (-) leads can actually be connected anywhere and it'll work just fine. Doesn't know, doesn't care where the power comes from!
Downside is it's inconvenient on a Pitts Special if I have to resort to removing the lower wing to gain access so I resort to mathematics (two switches) to make and break power. But for something like an Extreme Flight Extra where the entire top of the forward fuselage opens to expose the guts? Then I always resort to using extensions instead of switches because it's so easy to make the connections. Which lead is which? Doesn't matter, they're in parallel.
Last tip; do I always use LiFePO4 packs, or do I sometimes use LiIon? Facts are I use both and the answer to when is . . . it depends, once again.
Basically, for my scale models, like a giant scale P-51 Mustang or Dr.1 Triplane, large models where it's easy to size the servo torque to match the torque requirement 'and' I'm generally not needing the maximum torque available from a given size servo (meaning I can use a servo rated at 6.6V that meets the model's needs), then I use the LiFePO4 packs. Always. Why? because it's safer (meaning less risk of fire). And if we're being honest, for the convenience of being able to leave them fully charged because I'm as lazy as the next guy.
However, for models where I need the most powerful servo available at a given size, e.g. a 48" Extra? Then for this type/size model I'm going to opt the DS105CLHV sub-micro servo instead of the same size but less powerful DS75CLHV because I want everything I can get from a given servo-volume.
Why? Simple, because I want the most powerful servo available (to swing the relatively huge control surfaces with the authority required). So for 'small' models which require the highest voltage, my go to is the B2S850, a LiIon 2-cell pack that charges rapidly and importantly, allow a high rate discharge of more than 15A (850mA x 10C=16.5A).
- Not just one Dupont connector (worth 5A) but two, plus a 30A XT30
So for these 3D type aerobatic models (as opposed to a more sedate performance scale model like a Piper J-3 Cub) then I usually opt for the higher voltage LiIon pack because I want the most punch possible from the servo. And for that, there's no substitute for higher voltage and all else being equal, the LiIon will deliver more voltage than the LiFePO4 chemistry, capice?
Bottom line? High performance sometimes means inconvenience and thus, if I want the highest possible performance from the servo (true for any servo, any brand), then I have to accept the inconvenience of putting LiIon packs to storage voltage when I'm done using them.
Pro Tip: regarding LiIon vs. LiPo and LiFePO4 vs. LiFe . . . they're chemically similar to each other but the packaging is different. LiPo and LiFe use a flat orientation polymer bag for the cell construction while LiIon and LiFePO4 roll the electrolyte and fit it into a metal shell.
The former are so fragile you can dig a thumb nail into one and damage the cell (or bump it against a the edge of former whilst installing or even flying). Basically, 'any' deformation damages the electrolyte within the cell. However, the latter, because they're contained with a metal shell are far more robust. Tiny bit heavier? Yes, but it's the price I pay for my packs being more durable. Pick your poison!
Last thing, batteries are vulnerable - even the ones in metal shells. For this reason I use protection, e.g foam wraps on my packs, also.
Below are ones designed to protect expensive receivers, but they work equally well to protect battery packs. Yes, you can use inexpensive white foam rubber from the hobby shop but in my experience it degrades too quickly into dust particles. So my choice are these because they feature long life durable neoprene rubber (unaffected comparatively by UV), and which instead of being secured with rubber bands that also degrade, feature instead a convenient D-ring and Velcro-strap (below).
Note; I'll pass a zip-tie through the D-ring and secure it to a bulkhead to help keep pack or receiver from being tossed around by violent maneuvers.
We offer the latter type, PDR0046 Neoprene Receiver/Battery Wrap and it's our part number so if you click on the link, it'll open in a new tab.
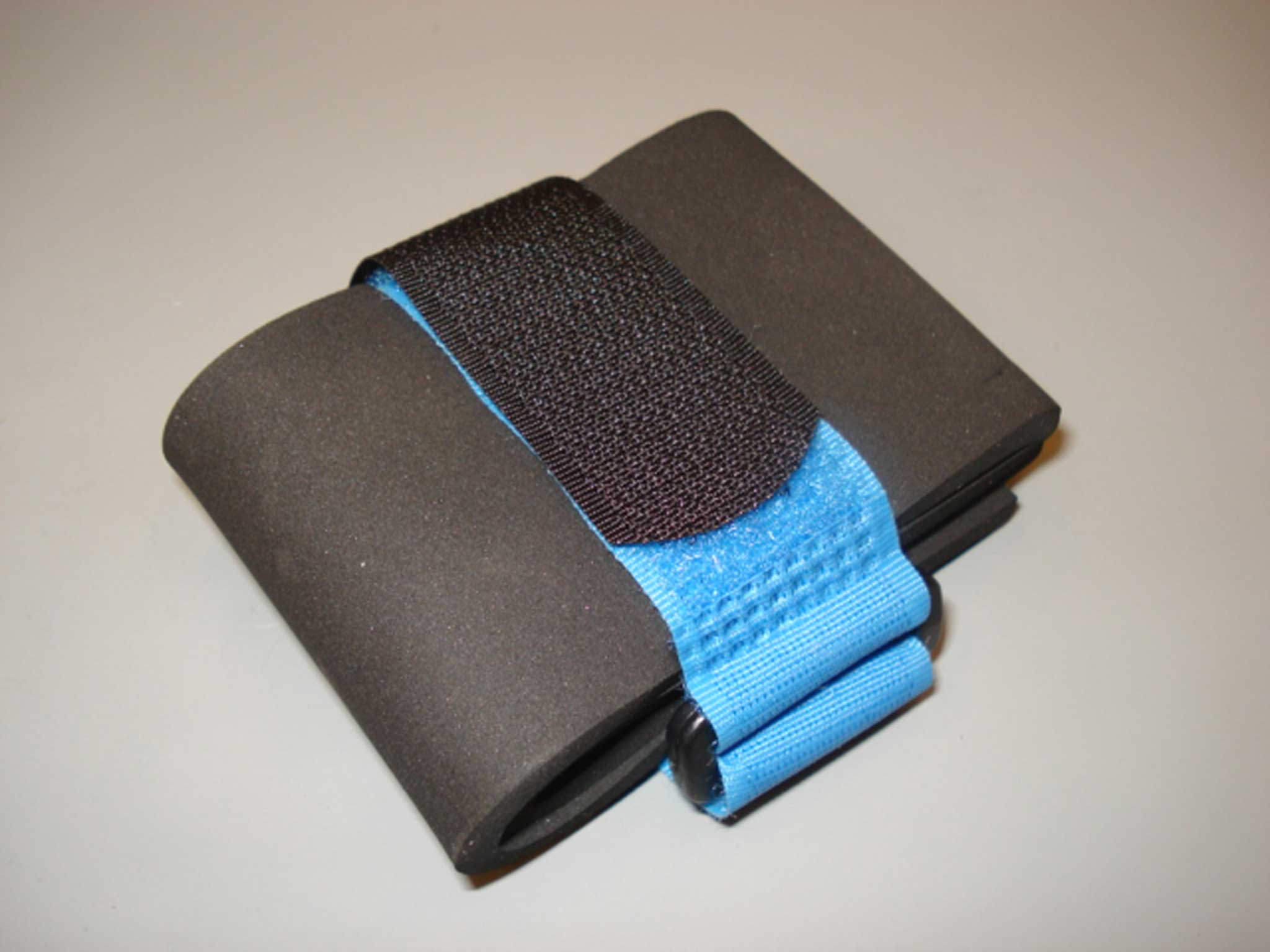